Durable Fabric Building Construction
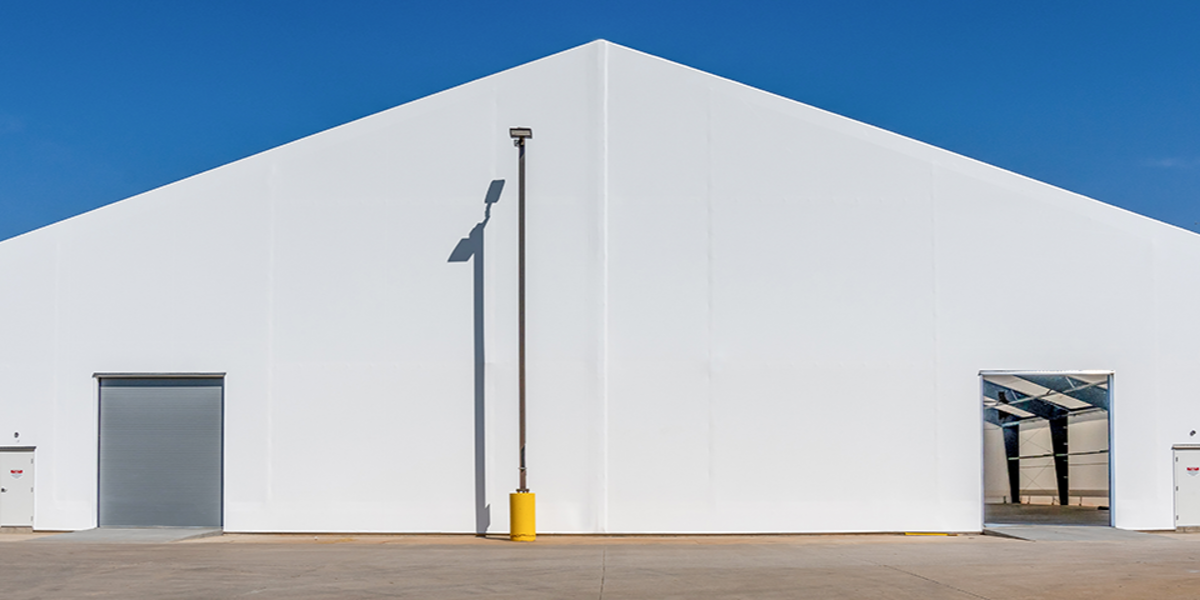
As manufacturing businesses grow, they need more space to house equipment and product, and they need it fast. Conventional, monocover fabric buildings are economical and simple to construct. However, they do not adhere to industry standards for extreme weather resistance. Therefore, if repairs are needed, the entire structure must be reskinned, which is costly and time-consuming.
Recent technological advancements in fabric building have been beneficial to the construction industry. It has allowed for designs that were previously unheard-of for every application.
AGC AUTOMOTIVE is a major manufacturer of automotive windshields and replacement parts for OEMs. As their Elizabethtown, Kentucky, location expanded, they needed significant additional space to store manufacturing equipment and tooling. Because they wanted the natural light of a fabric building, they considered putting up multiple buildings.
Legacy Building Solutions suggested one structure. It was 164 feet wide and 100.5 feet long. This resulted in a total of 16,482 square feet of storage.
Legacy engineered and installed one building with the necessary square footage for AGC's storage requirements. This saved time, money, and space that would have been needed for two buildings. The engineers used a custom-engineered rigid steel frame to build the huge fabric structure. This was combined with a unique multi-panel fabric attachment system.
“When people think of fabric buildings, they sometimes think of low-cost structures you can put up on a weekend. Legacy’s fabric buildings use the same engineering principles as other pre-engineered, metal buildings,” said Juliet Brambrink of Legacy Building Solutions. “They're a modern building solution that meets all building codes and other requirements.”
Advantages of Advanced Fabric Building Structures
Conventional fabric buildings are built with truss systems. These systems have limited design options, as they come in standard sizes. This prevents them from being optimized for specific applications.
Truss systems in wind or snow can cause conveyors and collateral loads to sway more. This leads to increased maintenance and downtime compared to when they are hung from a rigid frame.
Fabric buildings are built on a rigid steel frame. This frame gives them straight sidewalls, making the inside more useable. Also, different sidewall finishes can be applied, such as metal or precast panels.
Durability and Utility with Engineered Fabric
Legacy uses its own ExxoTec PVC fabric instead of the polyethylene fabric common to conventional fabric buildings.“ExxoTec fabric is a coated PVC with an inner scrim layer and three protective coatings on each side,” said Brambrink. “That coating is UV-resistant, so it's a really high-quality PVC material."
The fabric allows entry of natural light and is non-conductive, creating a cooler building interior in the summer and warmer conditions in the winter for reduced energy costs.
Legacy's fabric buildings can be insulated to meet local energy codes. HVAC and ventilation systems can also be added to the building frame.
Designing Fabric Buildings Around Your Application
Bulk storage, manufacturing and light industrial work are more efficient if the building is designed around the operation. “All different factors will impact the type of building you choose and the design of your building. These factors include how people and equipment are going to access the building, energy efficiency, and ongoing maintenance costs,” Brambrink explained.
When working with Legacy, an engineer reviews all building plans and factors that influence building soundness, proving correct loading and reviewing building location and purpose to calculate the base plate reaction at the foundation.
Legacy uses computer design and engineering software to include features such as lean-tos, offset peaks, overhangs and varying column heights to their designs. 3D renderings and blueprints are available to assist in the permit process.
Connecting with Legacy Building Solutions
Legacy buildings are designed using the same engineering practices and software used worldwide and is not dependent on an individual engineer calculating each part of the work.
Legacy’s teams of builders, designers and installers meet regularly to discuss potential improvements to building systems of all their fabric buildings.
Subscribe to our Blog
Recent Posts
- Speed vs. Quality in Commercial Construction: How Hybrid Materials Bridge the Gap
- Beyond the Bleachers: Designing Visually Striking Sports Facilities
- Why Architects Prefer Hybrid Steel Over PEMBs & Traditional Builds
- Building Innovations and Trends in the Mining Industry
- The Importance of Warehouse Storage for the Oil and Gas Industry