How to Maximize Profits and Efficiency with Fabric Buildings
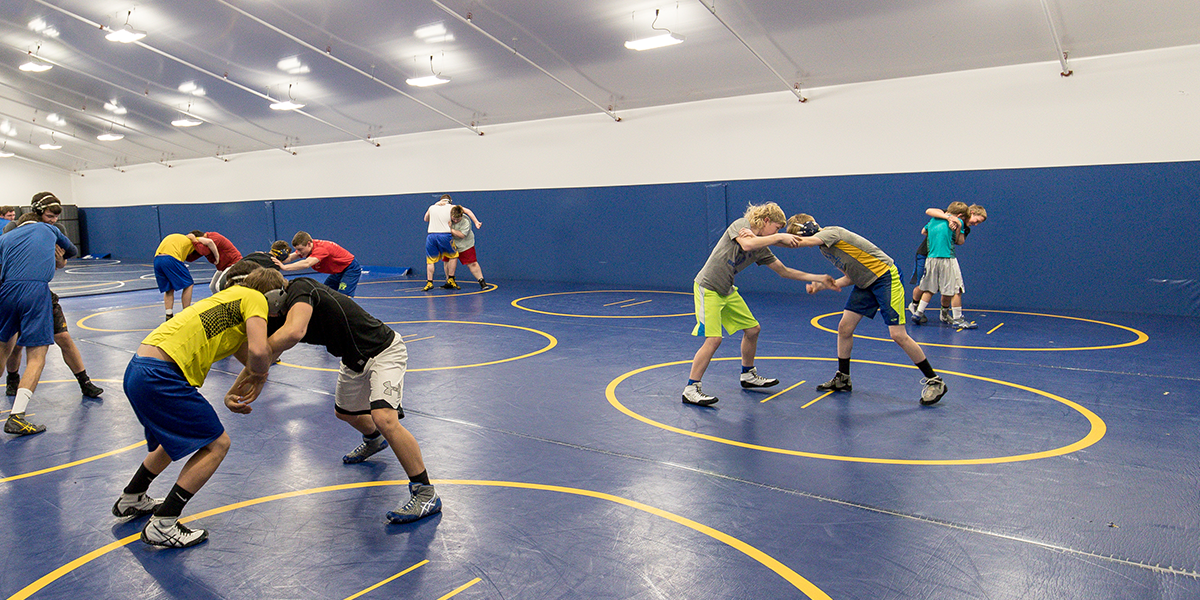
Fabric buildings are known as a cost-effective method of construction. The rapid installation, customizability, corrosion protection, relocatability and quality of fabric buildings are well established. But when making a capital investment, paying attention to the details can mean paying less over the life of the building.
How to Maximize Efficiency with Fabric Buildings
Heating and cooling costs are significant ongoing expenses. By maintaining a more consistent interior temperature, fabric buildings can reduce monthly climate control costs.
Unlike steel, fabric does not magnify the outside temperatures. Metal cladding will radiate the temperature variation, creating an interior that is colder in winter and hotter in summer. This creates an environment that is uncomfortable for people and animals, and increases the condensation build-up that often accompanies temperature swings.
Click here to learn how to control moisture in your building.
Flexible fabric also minimizes air leakage, resulting in a building which is much more efficient to heat and cool. Metal buildings are constantly contending with air leakage through screw holes and seams, which is often another avenue of heat loss within a building.
Fabric structures are known for having minimal air quality issues and lower‐than‐average building heating requirements. An independent study conducted on an insulated fabric structure by Legacy Building Solutions found it to be 157% more air tight than an insulated metal building. Fabric also allows for reduced air leakage through the wall assembly and fenestrations.
Learn more about how fabric is installed without penetrations.
Depending on the location and use of the building, Legacy offers insulation up to R-30. Insulation is installed between two layers of fabric to enhance the building’s ability to maintain a consistent ambient temperature.
Because of the air tightness and thermally nonconductive properties already noted, our insulated fabric buildings often cost significantly less to heat than comparable insulated metal buildings, creating long-term operating savings for their owners.
Fabric Buildings Have Reduced Maintenance
Building maintenance is a costly endeavor that is unfortunately necessary in many industries. Paint, shingles and siding all require regular maintenance to stay in working order and keep a professional appearance.
Engineered buildings avoid many of these requirements. Both pre‐engineered metal and fabric buildings are built to last for decades. The engineering behind these structures makes them likely to withstand everyday use and common hazards including snow load, strong winds and seismic activity.
Why are fabric buildings better in extreme environments?
Maintenance is one area where fabric structures often outperform steel. The steel sheets are inflexible and assembled with penetrations – over time, this will cause leaks. Fabric sheets are permanently welded together. Using Legacy’s patented fabric attachment system, individual panels are sealed together with friction‐fit overlapping seals to ensure that there is no air or water movement.
Repairing Damage to a Fabric Building
In industrial applications, the “give” of fabric also provides some protection from collision. When the fabric is damaged, it is easy to repair by the building owner or by trained crews.
Heat welding or a simple patch will restore the fabric to nearly 100% of its original strength. Most fabric building repairs are completed quickly to minimize downtime and return to working order as soon as possible.
Of course, all buildings are vulnerable to damage, whether from collision with heavy equipment, fire or extreme weather conditions. Fabric structures using Legacy’s patented attachment system ensure that in the unlikely event a section of the fabric is damaged, only the damaged areas need to be replaced.
Advantages of a Fabric Building Roof
On a fabric building, each roof panel is welded together to create a waterproof, sealed exterior membrane. The roof is the first line of defense from precipitation, making this part of the building critical for maintaining a dry interior.
Legacy’s system uses horizontal mechanical tension to stretch the fabric roof panels to the recommended level, keeping it taut and preventing friction for the life of the building. This system provides regular support and tension for the fabric both vertically and horizontally, which is critical to ensure a wrinkle‐free finish and a long fabric life.
See more advantages of a fabric building roof.
The advantage of a sealed fabric roof system is that the cover is completely waterproof. There are no tiny holes from bolts or screws like on a metal building roof, which can allow future drips and leaks inside. And because the panels are sealed together, there are not leaks at the panel breaks because of negative pressure inside the building at the keder locations.
Want to learn how to maximize profits with a fabric building? Contact us.
Subscribe to our Blog
Recent Posts
- Climate Resilience in Commercial Construction: Why Traditional Methods May Not Be Enough
- Speed vs. Quality in Commercial Construction: How Hybrid Materials Bridge the Gap
- Beyond the Bleachers: Designing Visually Striking Sports Facilities
- Why Architects Prefer Hybrid Steel Over PEMBs & Traditional Builds
- Building Innovations and Trends in the Mining Industry