How a Turnkey Fabric Building Supplier Can Save Time & Money
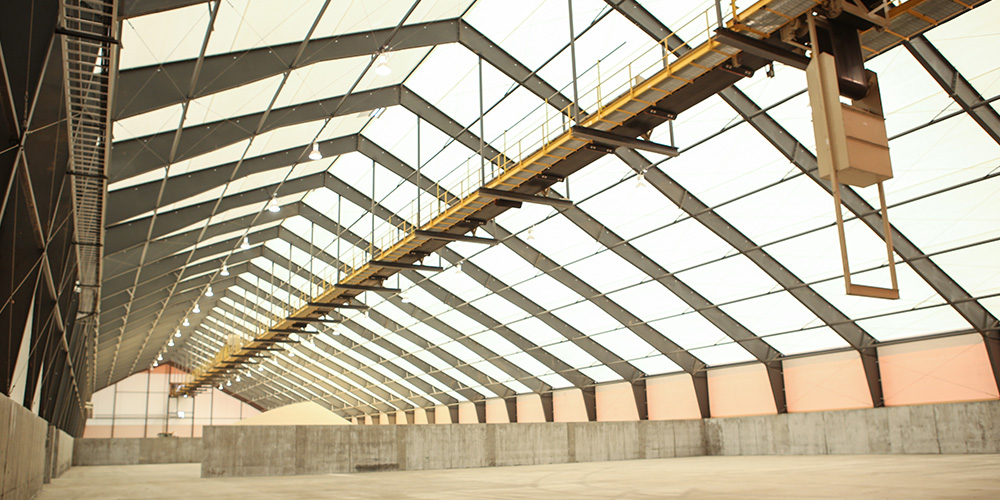
The staff at engineering.com recently profiled the advantages of fabric buildings, particularly for industrial applications and remote locations.
Manufacturers know that quick-to-build facilities for factory space or storage present unique challenges in their construction. Will a clear span for tall machinery and long production lines be necessary? How can operations be established in a remote or difficult location?
These requirements and more add complexity to a project, and the longer it takes from breaking ground to operation, the greater the costs in both construction and lost productivity.
So, what’s the solution? A turnkey supplier of fabric structures can provide cost savings to tough structural challenges, such as clear span requirements and working in remote locations.
Requiring a High Bay Height and Wide, No-Column Span for Production Equipment or Storage
Historically, manufacturing plants with space free from support columns tended to be very long, but were limited in width by the available span of trusses for roofing.
Columns are difficult for manufacturers to work around, because they significantly constrict the ways in which a plant’s machinery and production lines can be laid out. This creates issues for everything from on-floor material handling to safety – especially when the structure can’t support the load of systems such as overhead cranes, lifts and trolleys.
Clear span structures, also known as free span or open span, feature no interior columns. This allows for floor plans that can accommodate complex production lines and storage of large vehicles or equipment, such as airplanes, mining, forestry and transportation equipment.
Custom Fabric Structures Can Be Engineered for Any Height and Width
Fabric and steel frame structures offer an ideal solution to the challenge of clear span structural requirements. A company such as Legacy Building Solutions can offer highly engineered open-span tension fabric structures that will allow any facility to use the most advantageous and efficient layout for their production lines.
“We can go 400 feet wide without support problems, and that’s at any length and any height,” said Ben Fox, President & CEO of Legacy Building Solutions, a provider of industrial fabric structures.
Clear span buildings adhere to the same rigorous safety standards and building codes as conventional column-supported structures. In a properly engineered clear span building, the weight of both the building, as well as any additional weight placed on the structure, is transferred to the walls and foundation. Legacy’s engineers can help custom design a clear span building with the same flexibility as conventional structures, including adding large doors and supporting hanging loads such as cranes and overhead conveyors.
“Our fabric cladding and steel beam design allows for unlimited design flexibility,” said Fox. “This includes adding, cranes and conveyors, catwalks and so on. From the initial concept through the fabrication and installation, we take care of every step and can really customize to the needs of each structure.”
This flexibility means that it’s easy to add on to an existing fabric or brick and mortar structure in order to extend space for operations, whether it is to add new production lines or new machinery, or to expand the overall operations.
Having a customized, clear span fabric building will therefore save money and time by allowing manufacturers to plan and utilize the most efficient plant layout possible.
A great example is when the best production floor plan requires that tall equipment be situated somewhere other than along the center line.
“If you need an offset peak, for example, to position a conveyor in a better location, we can engineer the structure, so that the building peak and your conveyor are exactly where you need them,” said Fox.
Also, the materials used in fabric structures are easily packed for transportation to any build site.
“The fabric is rolled into bundles, and we would put them on a truck and transport them to any location, no matter how remote,” Fox said.
Remote and Off-Grid Locations Introduce Environmental Challenges
However, construction challenges may not come from what’s inside a structure, but rather what’s outside. Facilities may need to be close to outdoor operations – wherever those operations are located.
Building in remote or harsh environments can involve environmental factors that must be taken into consideration. Temperature, rainfall, snowfall and intense sunlight need to be compensated for in the design process. Other locations may have unstable sandy or rocky ground.
The last consideration is whether the operations are far away from critical infrastructure such as power grids, leaving no easy access to electrical power.
Building in remote areas can therefore be both costly and time consuming. Finding construction companies with the ability and willingness to work in these areas can be challenging, especially when one contractor can put in a foundation, but another contractor must be hired to build the structure itself.
Read the rest of the article here.
To learn how fabric structures may be the solution for your project, contact us.
Subscribe to our Blog
Recent Posts
- Speed vs. Quality in Commercial Construction: How Hybrid Materials Bridge the Gap
- Beyond the Bleachers: Designing Visually Striking Sports Facilities
- Why Architects Prefer Hybrid Steel Over PEMBs & Traditional Builds
- Building Innovations and Trends in the Mining Industry
- The Importance of Warehouse Storage for the Oil and Gas Industry