The Whole Nine Yards: Going the Extra Mile for Customers
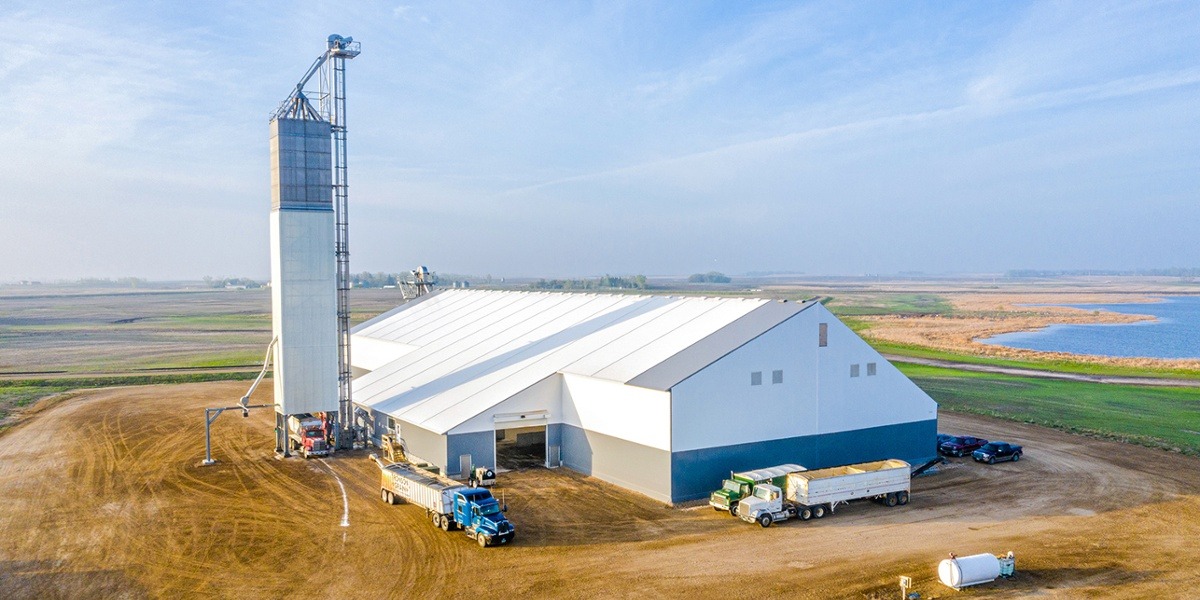
In the world of fabric, “the whole nine yards” was a phrase that indicated a job was done right. The “proper” suit created by a tailor would use nine yards of fabric, so that was the benchmark for a fine suit.
Here at Legacy, we go the whole nine yards for our customers when it comes to tension fabric structures, and we’ve got some examples to share with you.
Click here to see what some of our other customers had to about
Legacy Building Solutions.
Fishing for a solution
A Canadian company needed three of our tension fabric structures for their salmon farm. One of the buildings, however, required a low peak on the roof with a very gentle pitch. Consequently, our designers did what they have rarely done before: they designed the structure with a metal roof, fabric sidewalls and an interior fabric liner to provide protection from the salt water within the structure. Legacy is rightfully proud of our properly tensioned fabric roofs and all the advantages they provide for the building owner, but in this case, the best solution was a steel panel roof that would meet their requirements.
The customization didn’t stop there. With an insulated building, we typically install an interior liner, but this structure needed more than that. Cleanliness cannot be compromised in fish farming, so each tank needed its own sealed space. We created a series of interior fabric walls that ran throughout the space to keep each area separate.
Special Orders Don’t Upset Us
We did two cargo buildings for Ontario International Airport in California. James Kesler, head of cargo and development, asked for building that met his needs and met FAA regulations. Since the structures were close to the runways, the height of the buildings had to be limited to accommodate flights. However, Kesler wanted the building taller in the front where it wouldn’t affect the view from the air traffic control tower. “Legacy was the only one that could do a two-stepped building, so we could have a high part in front …and then have it stepped down, so we stay out of the clearance zone,” said Kesler.
You need it when?
In some cases, the ability to turnaround a project quickly for a customer has made all the difference. A biosolids composting structure in Southeast County, FL is a case in point.
We partnered with TLC Diversified, a water treatment and management contractor to complete this project. Original plans suggested the project be split into two buildings, but because of Legacy’s use of solid steel frames, we could make the entire project into one building of 139,750 square feet. That’s about 3 acres completely covered by our structure.
This composting facility had to be done, start to finish, in six months. That was the requirement from the county. Our combined teams collectively analyzed the necessary actions that needed to occur, and with communication and support from all parties involved, Legacy decided we could make that timeline.
In fact, we thought we could do better than that. A project manager from TLC said, “The thing that impressed everybody was the fact that Legacy came through and said, ‘hey we are going to better our time as far as manufacturing and shipping.’ And if I remember right, it was at least by a month.”
The installation was done in the six-month timeframe.
Other challenges that the team faced were poor soils, more slope than they anticipated, and a very rainy “rainy season”. Dalas Lamberson, vice president of TLC, said that a lot of the success of this team effort was due to communication. The urgency of the project had everyone answering their phone right away. “We all had our problems, but we found solutions quickly,” he said. “It was exciting to build it in six months.”
In the Words of Our Customers
Of course, hearing from our customers is the best. When they take the time to comment on our service or the quality of our construction, it ripples through the organization. For example:
“It was a priority to get the new building operating quickly so we could continue our programming. They were totally committed to doing whatever was necessary to support our project.”
- Steve Henry, OKC Tennis Center
“Our transportation system requires the diesel buses to be stored in a facility to keep them warm and protected from the elements. Legacy’s customized fabric structure design was able to fit our purposes. It was a good experience working with Legacy. Their in-house installation crew put up the building very quickly. They’re easy to work with and willing to help, and the communication with the city and responsiveness throughout the project was very good.”
- Joe Balge, Davenport Department of Public Works.
Exceeding our customers’ expectations is what gets us up in the morning, and it keeps us going every day of the week. The fabric and steel that make up our tension fabric structures are of the highest quality, but our ability to go the extra mile for customers is also what sets us apart. Let us prove it. Let us go the whole nine yards for your organization.
Subscribe to our Blog
Recent Posts
- Climate Resilience in Commercial Construction: Why Traditional Methods May Not Be Enough
- Speed vs. Quality in Commercial Construction: How Hybrid Materials Bridge the Gap
- Beyond the Bleachers: Designing Visually Striking Sports Facilities
- Why Architects Prefer Hybrid Steel Over PEMBs & Traditional Builds
- Building Innovations and Trends in the Mining Industry