Need a new Building? 7 Steps to a Good Decision
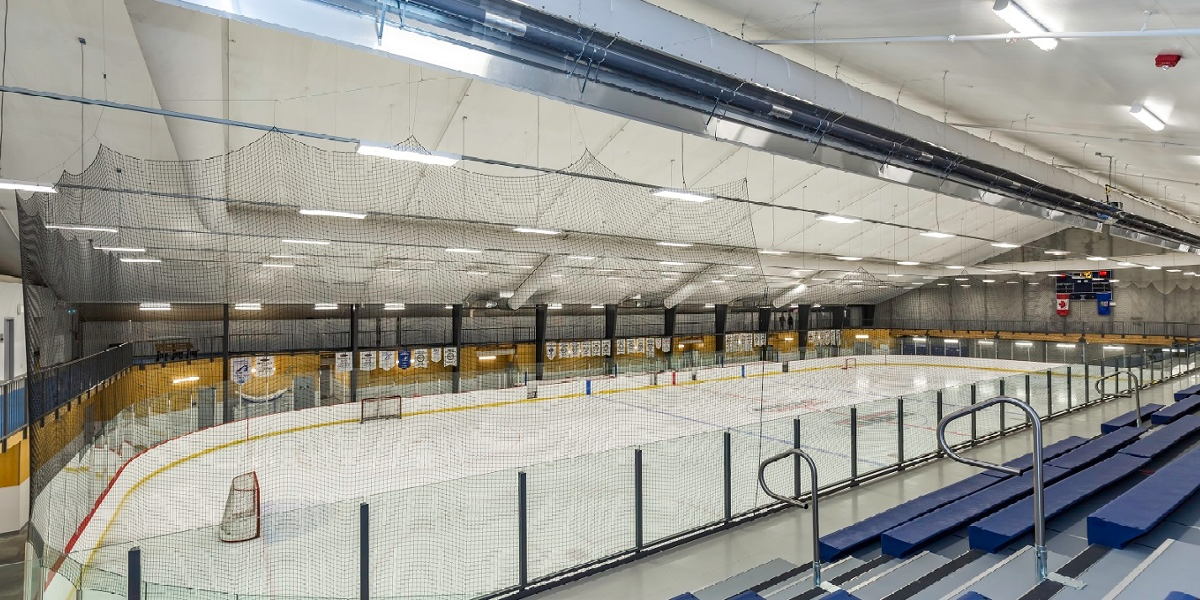
There’s an old saying: “Good judgment comes from experience, which comes from bad judgment.” When planning and designing a building, however, architects don’t have the luxury of learning from mistakes—they need to get it right the first time.
Every decision you make shapes the success of the project. Whether you’re balancing space constraints, climate control, or local building regulations, you need to avoid costly missteps and ensure a smooth design process from start to finish.
Here are seven key considerations to guide architects through the design process.
Step 1: How Big and How Much?
Do you know how much square footage you need? Your budget and application might determine that.
- For example, military hangars have strict width and height specifications, based on the wingspan and height of the aircraft being stored.
- In other cases, clients and designers negotiate before establishing the final square footage.
- Think about how much room you need for your storage or equipment, and how much “workaround” room you need. Just packing everything into the smallest possible footprint might saddle you with an unworkable space.
Affordability also matters. Your ideal structure in terms of size might exceed your budget, so be flexible.
- Always calculate the total cost of your building. The cost of the structure itself isn’t the only expense. A building project has a lot of incidentals that add up fast. The cost of digging, laying the foundation (plus reporting), windows, doors, HVAC, fire suppression, electrical, plumbing, etc. can make up the majority of a project’s cost. The structure itself can be a fraction of the total, sometimes as low as one-third of the costs incurred.
Step 2: How Warm/How Cool?
Fabric buildings can be open-air, like a large shade structure, or completely closed and insulated like a traditional structure.
- If you need to control the climate inside your structure, consider using completely insulated buildings for the hottest and coldest climates (and everything in between). If you don’t need the structure to be insulated, you can still benefit from the natural light that can come through the fabric roof and walls.
Step 3: Permanent or Temporary?
When choosing between a permanent or temporary structure, your decision may impact the foundation you’ll need. Permanent structures will ideally use a poured concrete foundation. Temporary structures may use earth anchors, or other solutions, for their foundations.
- Contrary to common belief, fabric buildings can be used for temporary and permanent applications.
- Legacy buildings have warranties on the fabric, steel, and construction that enforce that stability. That said, you can still design with the intent to move structures from one place to another.
One warning: some building owners want to label their structure temporary to avoid real estate taxes. That can backfire if you don’t check with your local building regulators first.
Step 4: Will it Support any Hanging Loads?
Think about the building’s intended use–will you need to design it to support large hanging loads, like cranes, conveyors, scoreboards, or stage lights?
- Some fabric buildings have a steel or aluminum support structure, only designed to support the walls and roof and limiting the ability to include hanging loads.
- Legacy’s steel structure can be designed to support a wide array of equipment.
Also, consider whether the building needs to support fire suppression equipment. More structures are required to have fire suppression systems, and that sometimes catches building owners off guard.
Step 5: What Kind of Fabric?
There are primarily two kinds of fabric in the fabric structures industry: Polyethylene (PE) and Polyvinyl Chloride (PVC). PE is used widely. PVC fabric is tougher and stands up to UV rays better. Legacy’s proprietary fabric, Exxotec™, is a PVC fabric.
There is also coated fiberglass fabric, but that tends to be costly and meant for very high-end use cases, like roofs of football stadiums.
Step 6 – What Foundation Type?
Don’t make the mistake of installing a foundation without doing due diligence about what’s under it. Many projects are delayed by bad soil under the foundation, so spend the time and effort to complete borings and soil reports. This is not the time to skip a step. If your foundation engineer doesn’t require soil testing before designing the foundation, ask some pointed questions.
Step 7: Talking to Building Officials?
Do this early and often. Don’t get blindsided by requirements from local building regulators late in the project. Communicate with local officials throughout the process. Remember, these officials will need to sign off on the designs, and they have final approval authority.
As you consider your next design project, keep these questions in mind. If you’d like to learn how a fabric structure can meet your needs, request a quote and get started with us today.
Subscribe to our Blog
Recent Posts
- Climate Resilience in Commercial Construction: Why Traditional Methods May Not Be Enough
- Speed vs. Quality in Commercial Construction: How Hybrid Materials Bridge the Gap
- Beyond the Bleachers: Designing Visually Striking Sports Facilities
- Why Architects Prefer Hybrid Steel Over PEMBs & Traditional Builds
- Building Innovations and Trends in the Mining Industry