Expedited Construction for Frac Sand Storage: A Case Study
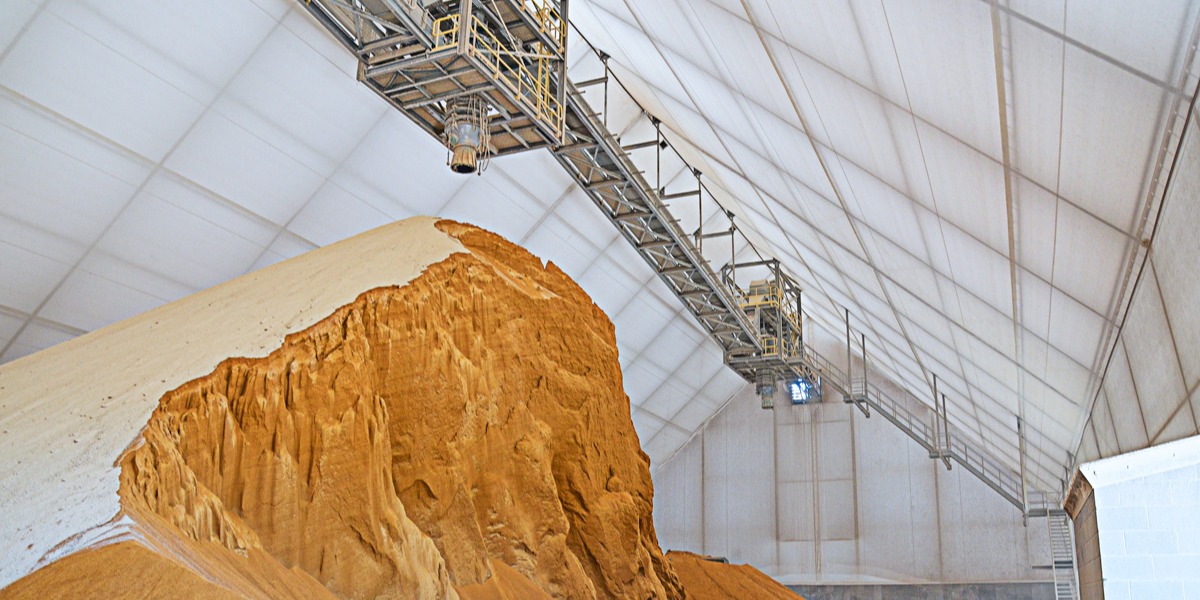
Being first to market is one way to establish industry dominance – especially an industry that moves as quickly as fracking. But being first isn’t enough. If you are first and unprepared, it’s easy for competitors to take your market share. The key is to be the first and the best prepared.
One important aspect of infrastructure: space. Specifically, cost-effective storage space and a way to move product in and out. Many locations require silica to be contained. A flat storage building keeps sand under cover during storage as well as loading and distribution. But traditional steel buildings can take months to build, eliminating the first-to-market advantage.
Fortunately, by eliminating or reducing common delays and using expedited construction, Legacy Building Solutions can have a fabric structure for frac sand storage designed, manufactured and installed in just a few weeks.
Fabric Structure Design Services
The Legacy team has in-house estimating, design and engineering departments. This means that with client cooperation, building drawings and plans can be completed, approved and stamped in a week or two – along with an accurate budget and construction timeline.
Legacy’s process focuses on helping the customer reach the end goal.
Vertical integration of services also provides clear communication. From these beginning stages through post-construction, you will have one point of contact who will have knowledge on the building’s design, manufacturing and installation. Rather than making multiple phone calls, juggling multiple timelines and dealing with multiple opinions, you’ll receive accurate information with one call or email.
In-House Manufacturing
After the building plans are completed, component manufacturing begins. The fabric and steel members are fabricated in house for tight quality control and timeliness. In-house manufacturing means there is no relying on a third party and a third-party schedule to start and complete manufacturing. And with on-hand inventory the Legacy crews can start fabricating building components right away.
Fabric manufacturing is completed to ISO 9001 standards. Polyethylene (PE) and polyvinyl chloride (PVC) fabric are manufactured in a climate-controlled environment to levels that meet or exceed industry standards.
Steel members are welded in the onsite steel manufacturing shop. All welds are inspected to meet AWS and CWB compliance. After components are primed, painted or hot dip galvanized after manufacturing. Learn more about the steel manufacturing process.
Expedited Fabric Structure Construction
Fabric panels are installed in about one-third the time of steel sheeting. This means crews arrive on site and complete construction faster than with traditional construction. Your operation will spend less time accommodating construction workers on site, and your building will be ready to go within just a few weeks.
Expedited construction means lower costs in addition to less time. You’ll save on hourly wages and living-out allowances for the crew, as well as using your building sooner for faster ROI.
Speed of construction is vital in emergency response situations. Check out other advantages.
In addition to the faster construction process, Legacy buildings are installed using highly trained in-house crews. Crews are on the road and ready to travel to any location for efficient, professional installation.
Full Service with Trusted Partners
Legacy Building Solutions provides installation services for our fabric structures. Depending on the project, we can also do foundation engineering and supply ancillary systems such as doors. For services our team does not provide, we partner with trusted entities who provide turnkey setups, allowing the customer to occupy a fully appointed building on a faster timeline.
Case Study: Pontotoc Sands
Pontotoc Sands Co. is a supplier of Tier 1 frac sands. Their El Reno, Oklahoma, operation needed an 8,000 square foot storage building to allow them to supply sand to nearby fracking operations. By partnering with Legacy, Pontotoc Sands had a completed building up and running in less than two months.
The president of Pontotoc Sands contacted Legacy on December 28. After determining the building specifications and providing a budgetary estimate, both parties signed the contract on January 12. Final building drawings were approved six days later, on January 18.
See the full specifications of the completed Pontotoc Sands building.
Component manufacturing started immediately, and components were trucked to the site from Legacy’s headquarters in Minnesota. Crews and supplies arrived onsite on February 7. Construction was completed and crews left one week later on February 14.
“From start of discussion until the building was loaded was less than seven weeks,” said Matt VanScoyoc, Legacy’s representative on the Pontotoc Sands building. “It was a whirlwind, but that’s how things tend to work in the fracking industry.”
Crazy construction timeline? Legacy Building Solutions can help you meet it. Request a quote to get started immediately, or visit us at Inland Marine Expo booth 517-519.
Subscribe to our Blog
Recent Posts
- Climate Resilience in Commercial Construction: Why Traditional Methods May Not Be Enough
- Speed vs. Quality in Commercial Construction: How Hybrid Materials Bridge the Gap
- Beyond the Bleachers: Designing Visually Striking Sports Facilities
- Why Architects Prefer Hybrid Steel Over PEMBs & Traditional Builds
- Building Innovations and Trends in the Mining Industry