Lessons from the Field
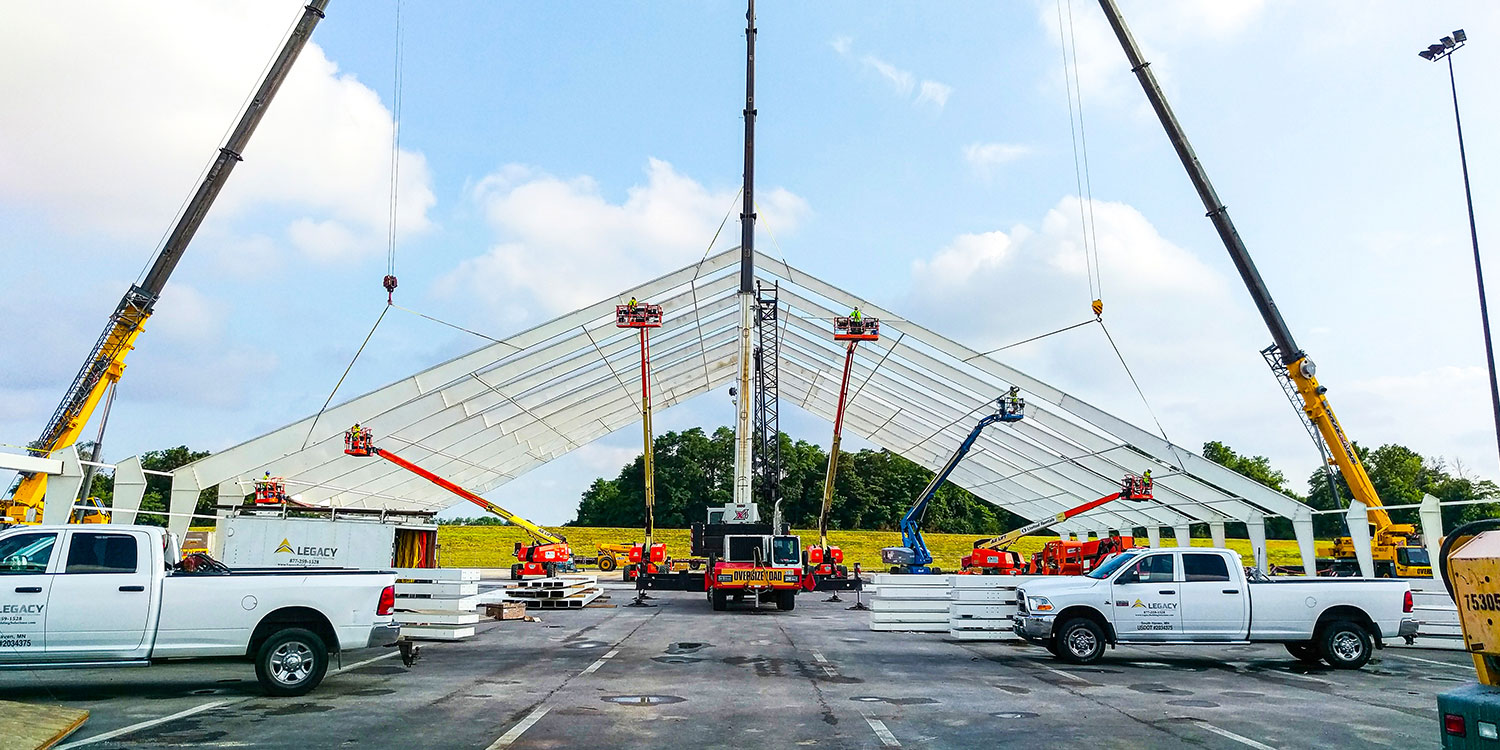
We talk about our crews a lot. That’s because we hear from our customers how impressed they are with our installers’ attention to detail, their work ethic and their safety practices. They are our road warriors, traveling all over North America, and the world, installing our tension fabric structures.
There’s a strong connection to our crews because what we do at our headquarters—designing, manufacturing, testing and even billing—affects what they can do out on the site. Fortunately, we have a number of former installation crew members here at Legacy. You never know where you might run into a former installer. Our CEO and founder, Ben Fox, was an installer of fabric buildings before forming Legacy.
Communication from our installation crews is vital. Ben said, “one of the biggest benefits of Legacy is the daily communication or daily feedback on the quality and constructability of our buildings. That helps the sales team, helps the design team, helps the manufacturing team to continue to improve.”
What our crews—both past and current members--learned from their site experience is the kind of real-world, deep knowledge that is irreplaceable.
Here are some examples.
Design and Tooling
“In my opinion, everything we do when designing a building is all from lessons that we learned in the field.” |
Our manufacturing manager, Jeremy Sanden, was an installer, and he says “the top thing that comes to our minds when we are figuring out how to design something new or make a current product better is how will it work while installing, or how the final fit and finish on the building will turn out with that design. It’s more than designing parts for the building: it extends to building tooling to make things easier for the install team. There are several specialty tools that we make in-house that we use to install Legacy buildings and make the job easier, safer and with better results.”
Ben adds, “We make all our own tools for tensioning the fabric--both horizontally and vertically--and how we terminate the fabric at the base. Those are tools that have their own nicknames.”
The fabric at the base, Ben explains, presented its own challenges because the tools they use on the rest of the building are too long. “You have that last little bit and that’s the hardest part of the fabric to get to look perfect—the tail is what we call it—and we’ve created tools to specifically tension that last little bit. There’s very little room to work with at that point.”
Quality
Sanden did installs, before Legacy was founded, for other fabric structure companies. He says, “quality control is a huge factor for me because I have been in the field and had to deal with missing parts, incorrectly made components or just faulty designs. All of those cost a lot of time and kill morale for the crew. When you are working away from home for weeks on end and have to wait on a part for two days, it is very frustrating. So making sure we do our part here, double-checking that everything is correct, eliminates someone else losing time away from their family.”
Almost every aspect of our quality control has been driven by the feedback we have received from our installation crews, says Ben.
Innovation
Jeremy remembers, “I clearly remember Ben calling me into his office along with other employees to talk about a new extrusion attachment system, shortly after we became Legacy. The first version that we had, took a lot of time to pull each roof panel on the building and had several different steps that needed to be done before moving on to the next panel. During this meeting, Ben began to draw on the whiteboard and said ‘let’s shoot holes in this and figure out why it doesn’t work’. At that point, you have to imagine each step as you were actually doing the work to find the areas that might not work. After that meeting and some R&D, the first version of our patented fabric attachment system was born. This led to a better design that we are using today. It makes it quicker and easier to install roof panels. Most importantly, it creates a better quality product and process for installing.”
“There are a lot of things that look good on paper or on a computer screen, but they don’t always work that way in the field.” |
Ben remembers that meeting and agreed that it was a key moment. The way keder rails were attached to the frames was a constant issue. Working this challenge out with folks who understood, first hand, how our buildings go together was invaluable.
Safety
What happens on the job site has also informed our approach to safety. Ben explains, “Honestly, the way we tension our fabric is far safer than the way competitors tension their fabric. When competitor tensions a fabric, they have to take brace members out of the structure to tension it and, as they tension it, put those brace members back in.”
“We can install fabric without ever having the building in a compromised position for a windstorm or weather event,” said Ben.
Legacy is proud of our installation crews—both past and present--and the way we operate as a company has been informed by the feedback from years of on-site observations and problem-solving. As Ben puts it, “When we do everything, from design to construction, and have that constant feedback, that’s how we can constantly improve and have a high level of quality.”
Subscribe to our Blog
Recent Posts
- Climate Resilience in Commercial Construction: Why Traditional Methods May Not Be Enough
- Speed vs. Quality in Commercial Construction: How Hybrid Materials Bridge the Gap
- Beyond the Bleachers: Designing Visually Striking Sports Facilities
- Why Architects Prefer Hybrid Steel Over PEMBs & Traditional Builds
- Building Innovations and Trends in the Mining Industry