Limited Budget, Limitless Imagination: Designing a Commercial Building with Monetary Restrictions
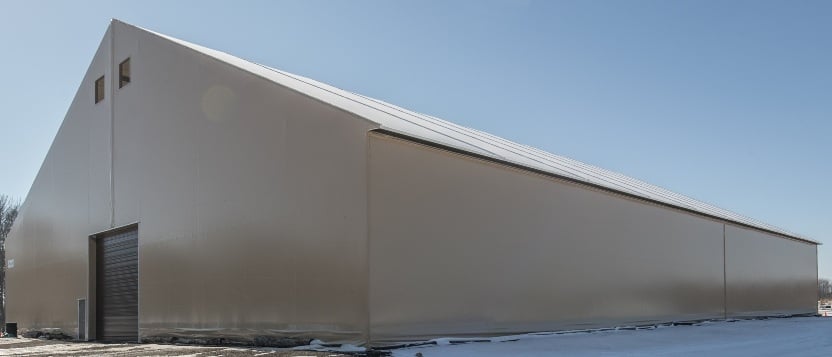
If you had an unlimited budget, you could build whatever you want–the commercial building design of your dreams. In most cases, though, the project budget dictates what you can or can’t create.
However, a limited budget doesn’t have to limit architectural creativity or sacrifice functionality, features, or quality. Choosing the right type of building can uncover fresh ideas to achieve the result you want.
That’s why we often see architects and owners consider fabric buildings for innovative solutions to commercial building design challenges.
How Much Should You Budget?
Engineering, materials, labor, construction costs, and time to completion all factor into a project’s budget. Everyone wants as much as possible, whether that’s a building that’s 20 feet wide or 300 feet wide.
Getting it right before you move forward helps eliminate costly delays, change orders, or functionality issues. If the budget is limiting your desired design, it’s time to get creative. Here are some examples:
Customized footprint
A right-sized building ensures sufficient space without over-paying for wasted space. Rigid solid steel framing is strong and versatile, allowing for clear-span construction with widths over 300 feet, unlimited length, and high roof peaks without the need for interior structural supports.
The ability to stack racking systems higher–and hang cranes, conveyors, or scoreboards from the ceiling–clears floor space for the work at hand. That often reduces the required footprint, saving money.
Configuration changes
Door types and placements affect engineering. If oversized doors are required to accommodate large equipment or aircraft, that increases building cost. On the other hand, changing the location–like putting a 30-foot door on an end instead of a sidewall–helps cut costs.
Because every Legacy structure is 100% custom-designed, we always work closely with customers to help set a budget and determine what can realistically be done within that budget. The collaborative team often includes in-house or third-party design team members as well as owners.
We work with our customers creating several preliminary iterations to fine-tune during the planning/design phase. By doing so much work upfront to optimize design, we can make the most of your budget and deliver an installed building far faster.
Shortening the Timeframe Saves Money
Having a single source point of contact can prevent communication misunderstandings and production or construction delays. A shorter timeframe can lessen the impact of volatile labor and materials prices that could increase costs. The sooner your building can be designed and built, the sooner you can start using it.
We offer a comprehensive, one-stop solution with our 8-step building evaluation and buying process. Once we understand your needs, wants, and problems so we can come up with design solutions, we handle everything else in-house:
- Engineering
- Manufacturing
- Ship to site and install
This streamlines the entire process and gets everything done faster.
Up-Front Cost Is Just the Beginning
Budgeting for structure design and construction is only part of the equation. Make sure to consider operations costs over the life of the building so you can achieve the lowest possible total cost of ownership.
Maintenance is a major factor. Metal and traditional wood buildings notoriously require costly, ongoing maintenance, while fabric buildings are mostly maintenance-free.
- The fabric rinses clean in the rain or with a quick power wash, so your facility always looks its best.
- Solid steel framing and EpoxxiShield™ epoxy coatings protect structures from all types of corrosion dramatically better than hot dip galvanizing.
- ExxoTec™ fabric cladding is highly durable and less likely to sustain damage from the bumps and bruises of working machinery.
- Sturdy fabric structures are engineered to reliably withstand harsh weather and extreme conditions, greatly reducing the risk of damage and repairs later on from hail, snow, hurricanes, earthquakes, and so on.
Because the engineering has already been done, fabric buildings can easily be lengthened in the future. You can also build an adjoining structure alongside. These features make expansion more affordable.
Sustainable Building Design Is Budget-Friendly
You can also trim long-term costs by investing in solar panels and sustainable energy options:
- Thermal non-conductivity keeps interior temperatures naturally more comfortable, reducing heating and cooling costs
- 12% translucence admits enough sunlight into uninsulated buildings to eliminate or greatly reduce the need for artificial lighting during the day
- The interior white fabric surface is naturally brighter and eliminates dark corners, again reducing the need for additional lighting
Stretch Your Imagination
In reality, structure design is limited by available space, regulatory requirements, and other factors that can directly impact your budget. But that doesn’t mean you can’t let your imagination soar to optimize design and budget.
If you’re struggling to fit your design ideas into a limited budget, reach out to our team. We can help you avoid mistakes and ensure no opportunities to control cost or enhance usability are overlooked.
Subscribe to our Blog
Recent Posts
- Speed vs. Quality in Commercial Construction: How Hybrid Materials Bridge the Gap
- Beyond the Bleachers: Designing Visually Striking Sports Facilities
- Why Architects Prefer Hybrid Steel Over PEMBs & Traditional Builds
- Building Innovations and Trends in the Mining Industry
- The Importance of Warehouse Storage for the Oil and Gas Industry