Single panel fabric structures versus Monocover buildings
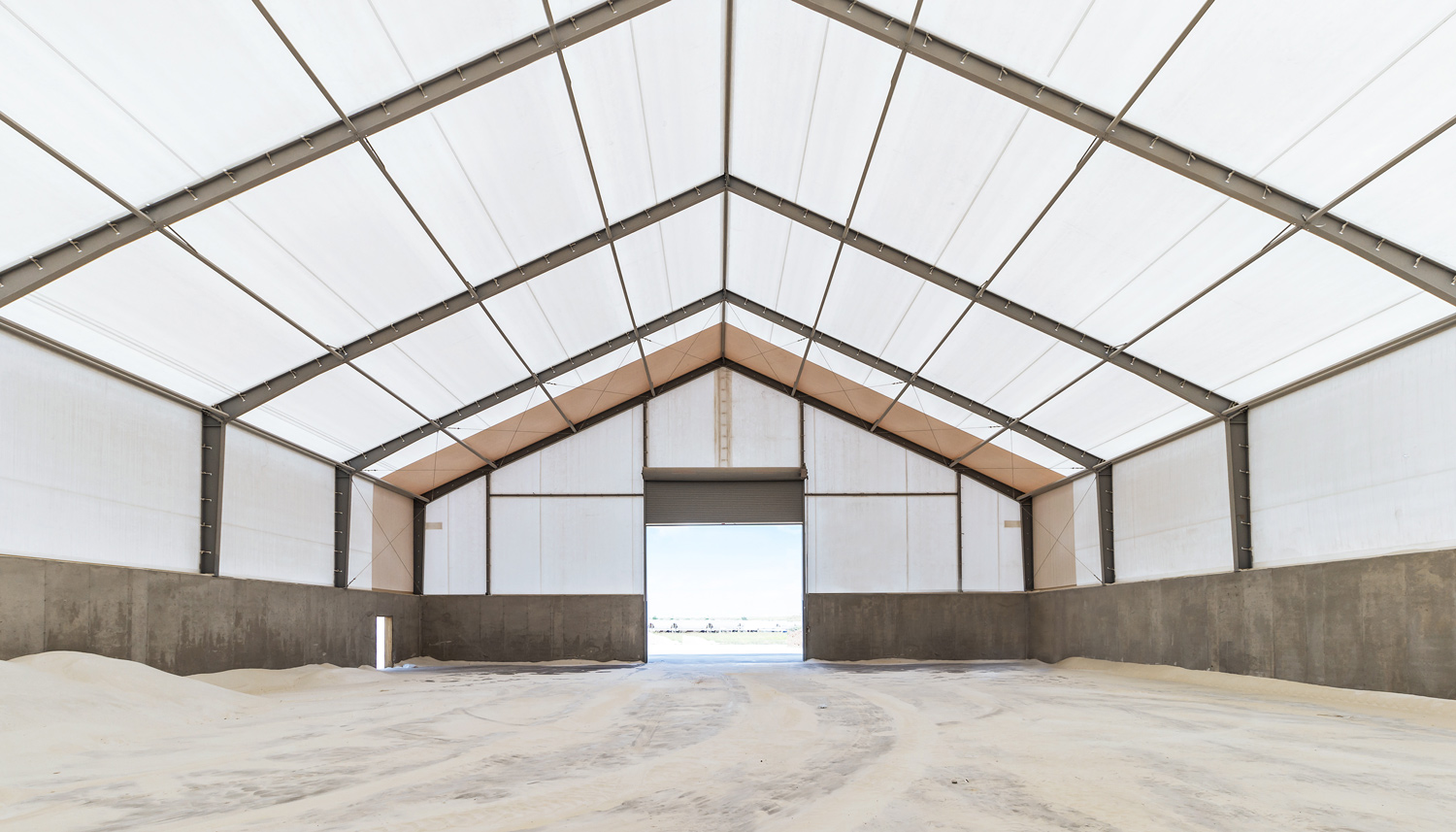
Before Legacy began operations in 2010, our team already had years of experience installing all manner of fabric structures. Many had been doing it since the mid 1990s, and they installed their fair share of monocover buildings.
A monocover building is typically a framework of supports with one large piece of industrial fabric stretched to cover the entire roof and sidewalls. Monocovers are relatively inexpensive and easy to construct, and they are still used by a number of fabric building manufacturing companies today.
When our team had the opportunity to go in another direction, they began researching and developing our tension fabric structures.
We knew that the longevity and durability of any building depended on the quality of the materials and the strength of their connections. Monocover buildings just don’t stand up to buildings constructed of individual fabric panels.
Weak Attachments
In a monocover building, the fabric is attached only to the building’s end frames. The middle building frames provide shape but the fabric is not connected to the frames and the full load applied to the fabric from wind is often transferred to the end frames instead of the individual frames.
When wind blows over the peak of a building on the leeward side, the fabric creates a suction and lifts off the structure, to the point where fabric is no longer touching any of the interior trusses. Fabric and frames are typically not designed to handle those forces without support, and these situations can cause the fabric to tear away from the building or the frames of the building to collapse.
Another disadvantage of using one large cover on a building is that if one section of the cover tears or fails, the entire building must be reskinned. This results in lost time while there is no cover on the building. Repairing or replacing an individual panel is a comparatively simple, inexpensive process.
Monocover Load Transfer
Monocover building covers are exposed to more friction than buildings with individual fabric panels because of the fabric movement over top of the frames that occurs during wind and snow events as there is no permanent connection to the frames. Over time, this friction will weaken the fabric, and can lead to thinning or tearing.
Separate Fabric Panels to the Rescue
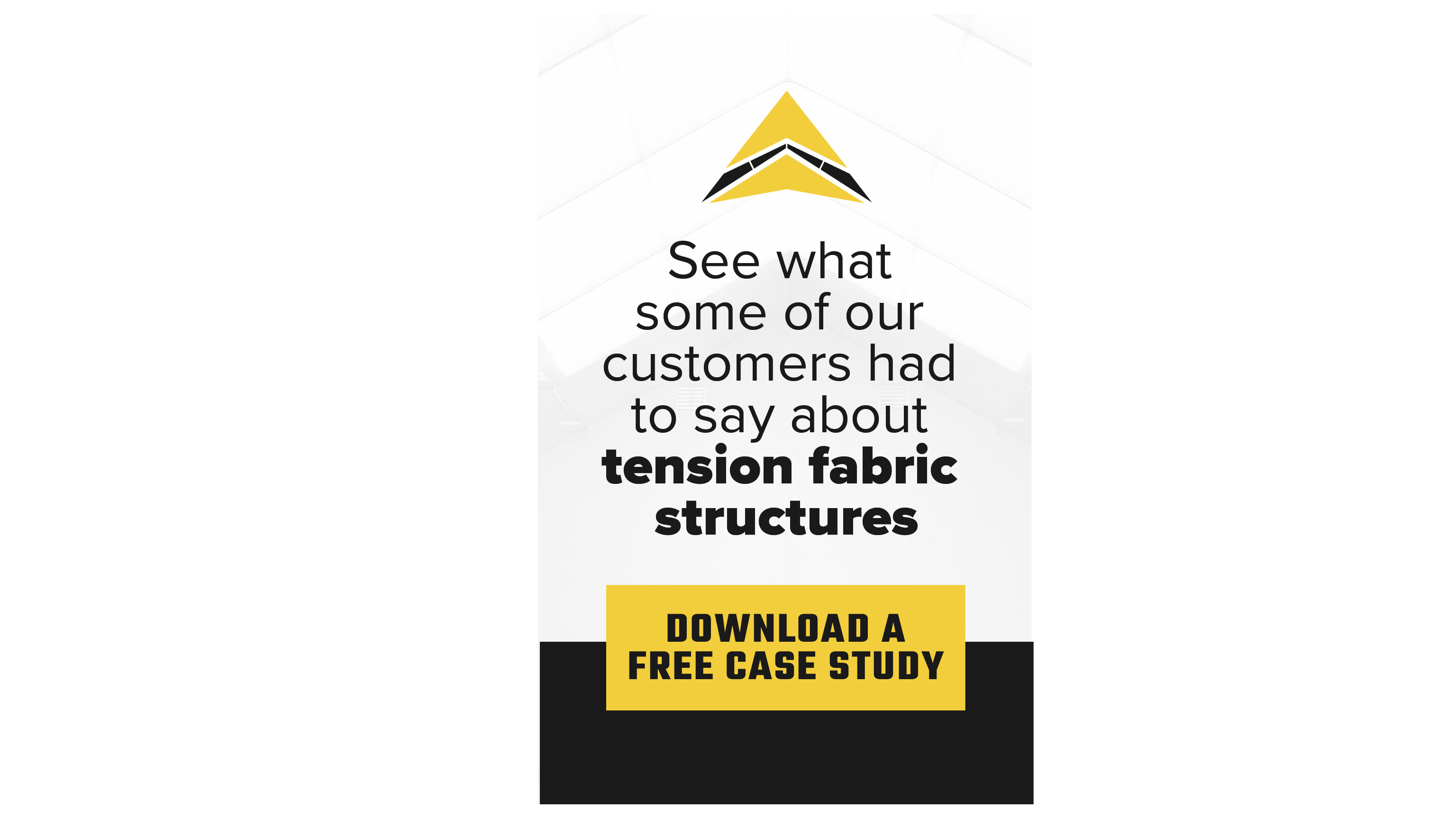
When you clad a structure in individual fabric panels, you eliminate a lot of the monocover problems right away. The fabric is securely fastened to each frame continuously creating engineering load certainty for both the frames and the fabric.
We already mentioned that fixing individual panels is much simpler and more cost effective than replacing an entire monocover. There is also the matter of tensioning.
Our fabric panels are tensioned differently. Without going into too much detail, the fabric is pre-tensioned via biaxial stretching and always kept flat. That reduces the amount of friction, which can damage the fabric over time. The physics of our Exxotec fabric lets our installers properly tension the cladding, adding to its long term durability. Finally, whereas most fabric structures require retensioning over the years—often multiple times—our individual panels do not.
On the engineering side, Legacy, with our tapered column rigid frame design, utilizes the same engineering design software as pre-engineered metal buildings (PEMB) which is used to design thousands of buildings around the world annually, which provides both Legacy and our customers with engineering certainty of the frame design.
On the look-and-feel side of the equation, our paneled buildings have a crisp clean look that comes from a combination of our proprietary PVC fabric and the way we tension it. Having straight walls, as well as pitched roofs with high peaks, makes our structures look exactly like traditional buildings (sometimes better) with all the advantages of a fabric building.
Installing a fabric panel building with all the correct tensioning takes training, skills and expertise. That’s why we use our own crews to install our buildings. They travel the world all year, installing our unique customized fabric structures.
Because our team had a lot of previous experience installing monocover fabric structures, they knew the drawbacks. They decided to do something different—a tension fabric structure using separate fabric panels. It has made all the difference for us and, more importantly, for our customers.