A Decade of Fabric Structures in Review
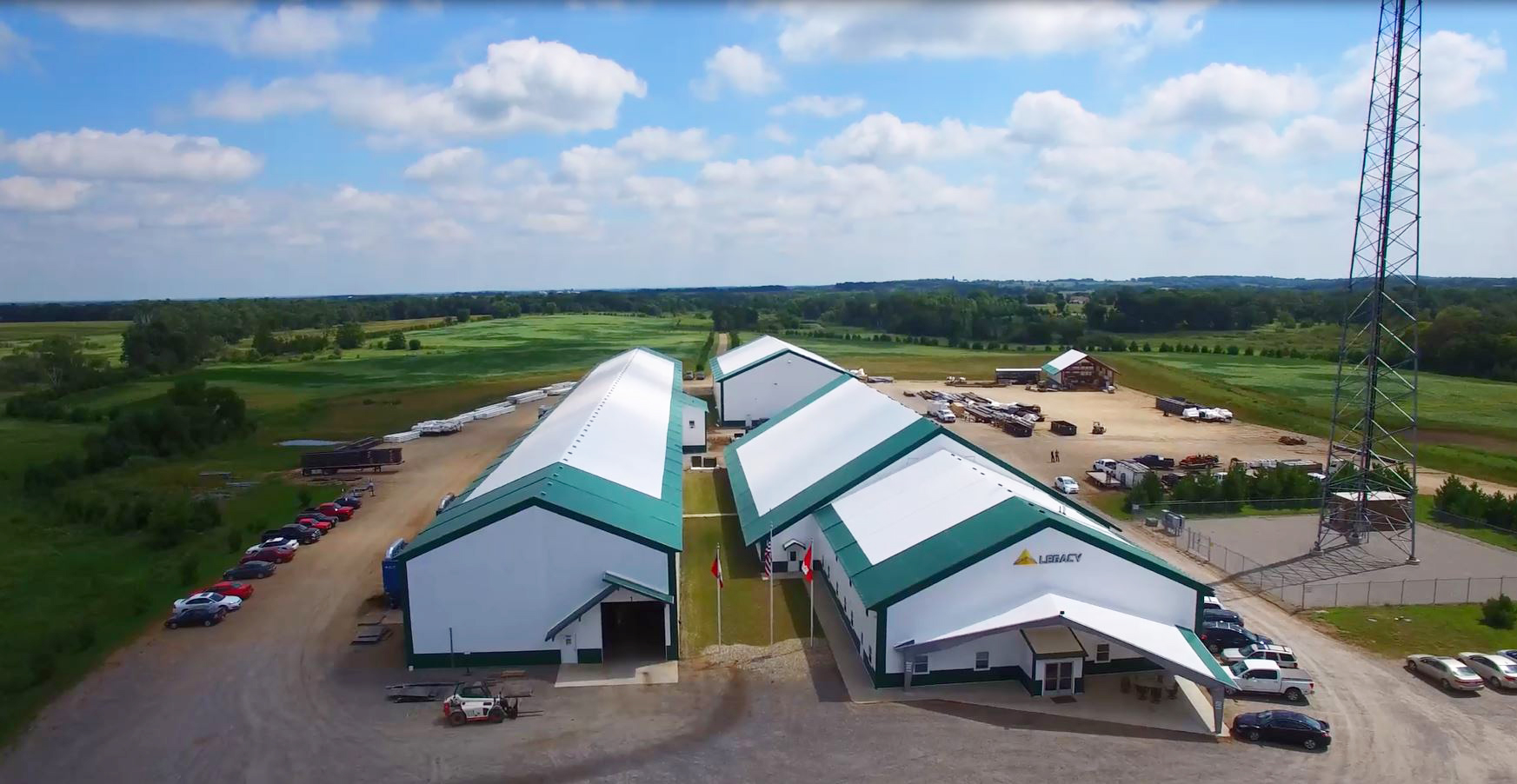
Thirteen years ago, Legacy started its business to revolutionize the fabric-building industry and change how fabric structures were designed, manufactured, and installed. Thirteen years and hundreds of buildings later, we took a look in the rearview mirror to see if we:
- Revolutionized the industry as we planned
- Met our own goals regarding quality, innovation, safety, and client satisfaction
This exercise prompted us to review our business holistically and take the time to understand each year’s innovation and lessons that accompanied each initiative. Below is an illustration of each milestone and what it meant for our team, purpose, and growth.
Learn What You’re Not
This helps you laser-focus on what you are so you can build and iterate off that one thing for years and years to come.
Ten Years in Tension Fabric Video Tour of Our Favorite Buildings
We design, manufacture, and install the tension fabric structure.
Sometimes it’s easier to say what it isn’t.
- It isn’t a tent
- It isn’t a bubble, meaning an air-supported dome
- It isn’t a mono cover
- It isn’t a web truss
- It isn’t a single-tube structure
- It isn’t a tensile fabric structure
Always Build Something Better
Legacy began operations in 2010, but the founders and many of the original employees had a great deal of experience installing fabric buildings—for other companies. The journey began with the notion that fabric buildings could be better, be different, and be something that would exceed our client's expectations. The look, the feel, and the structure of fabric buildings were due for a makeover, and Legacy was eager to reimagine the industry's future.
Ben Fox, the founder, wanted to make a better fabric building based on what he had learned while installing other buildings. In particular, he wanted to address a fabric structure's quality and long-term durability. He also wanted to design a building that looked like a traditional building with clean lines, a crisp exterior, an amazing interior, and an overall beautiful feel. Some changes the company made immediately, and some of the advances happened over time after working with the materials.
And just like that, Legacy Building Solutions was created. We are proud to continue building off of what we've learned.
1. Steel to Withstand
We always start with steel, which gets the number one billing in our innovation list.
One of the changes we made to the world of fabric structures is designing a frame of solid steel tapered I-beams.
There’s a lot to unpack there. First, solid steel meant two things to us: strength and engineering certainty. We could engineer a structure that could withstand wind, snow, and seismic conditions worldwide with solid steel instead of hollow tubes or web trusses.
Solid steel also opened up opportunities for us, as designers, and to our clients, as building owners.
Engineering Certainty
Engineering certainty meant a couple of things.
First, it meant that the tension fabric structures were aligned with the engineering standards of the rest of the world—meaning the world of traditional buildings. Our fabric structures meet or exceed the local building codes of the states as well as international building codes. Steel and engineering certainty allowed us to meet almost any standard.
Secondly, we designed our buildings with the same software used throughout the steel building industry. That standard meant almost any engineer could pick up our drawings and blueprints and instantly understand what we were doing. For example, if a local regulator wanted to take our designs to his county engineer to check them out, that engineer could read the blueprint without needing translation. To us, good engineering is not proprietary; it’s universal.
See: Steel Story—The ADM Ottawa vs. Derecho
2. The Weight of a Warranty
In 2016, Legacy switched its fabric cladding to ExxoTec™. Before that, the industry standard was polyethylene fabric. Our research into better fabrics and ways to do things revealed that PVC fabrics showed some promise.
PVC fabric was tougher, and it withstood UV rays better. We settled on a proprietary fabric designed for Legacy that was PVC scrim, covered with PVC film on both sides, followed by a layer of lacquer on both sides.
ExxoTec™ fabric is tough. It’s tough enough to allow us to give our cladding a 25-year warranty for our 28-ounce fabric. How do we know just how tough it is?
Well, we tested it.
3. Stretched to the Limit
Legacy uses proprietary materials in our buildings, but we also have a patented attachment system.
Our team realized that by using ExxoTec™, the physical properties of the fabric itself would allow our installers a better option for stretching the cladding on our frames. This stretching is called tension, another thing that makes our structures different.
Using Legacy’s patented attachment system, each fabric panel—typically 20 feet wide—is secured to the frame using a keder rail that slides horizontally on the top flange of the frame, eliminating the need to detach or flex frames during installation.
Instead of tek screws (which create possible failure points in the aluminum keder extrusion), we use bolts to attach the rail to the frame.
Wrinkle-Free & Long-Lasting
The system also uses horizontal mechanical tension to stretch the fabric to the recommended level, keeping it taut and preventing friction for the life of the building. There is regular support and tension both vertically and horizontally, which is critical to ensure a wrinkle‐free finish and a long fabric life.
There is also greater vertical or “up and over” tensioning because the fabric is tensioned in a straight line, not around curves or radii.
What this means for our clients is that Legacy buildings do not require fabric retensioning after installation. Other fabric buildings typically require retensioning of their fabric, not just once, but multiple times over the life of the building. Ours do not. When we talk about our structures being virtually maintenance-free, our patented tensioning system is one reason.
4. Corrosive Environments
Some of Legacy’s earliest buildings involved salt storage, mining chemical storage, and fertilizer storage.
We took an early interest in corrosion because many of our clients had very corrosive environments due to the materials they stored. Our steel is very important to our structures, so protecting it became a focus for our company.
For many years, hot-dipped galvanizing (HDG) was the answer. That method slowed down the corrosion significantly but didn’t technically interrupt the corrosion. That’s one reason we began to look to expand our product offering to include epoxy coatings.
We have clients who require the best corrosion protection. In the case of the mining sector, we are working on a project in which copper concentrate will be stored. That reacts chemically with galvanized coatings, so epoxy was the solution that precisely fit their needs.
We committed to providing epoxy-coated steel to our clients for a couple of reasons:
- Better corrosion protection than HDG
- Easier to repair if the surface is damaged
5. Our Own Installers
Before Legacy was launched in 2010, many of our associates worked installing the buildings of other companies. We have a long tradition in fabric building installation, leading us to our own tensioning system mentioned in lesson three. That tradition also convinced us that using our own crews to install our structures was vital to the company's success.
Legacy does things differently. We needed experienced, well-trained installation teams to implement our processes. It wasn’t something we could farm out to sub-contractors or local construction teams. Getting the installation right was absolute; the processes we built into our structures required the best teams possible, period.
Road Warriors
Our installation crews travel the North American continent—and the world—installing our buildings.
When an installation team shows up, they are ready to work, often working long hours and during weekends. They have also trained in our own safety requirements as well as the safety requirements of our clients. We often get comments from our clients about their work ethic, reliability, and attention to detail.
One of the comments we get, again and again, is how fast our crews can put up a building. Often our crews can install a building for a client in days or weeks, not months or years. They can do that because we, as an organization, have streamlined every step of the building process. We do all of the design, the drawings, and the contracts, as well as the manufacturing of both the solid steel frames and the fabric cladding.
End-to-End
Because we do almost everything in-house at Legacy, we control the logistics. That means those in the steel manufacturing plant will ensure the right parts are on the truck and, more importantly, that the steel is stacked in the right order. You can imagine how much faster a crew can proceed on a building when everything—steel and fabric cladding—comes off the trucks properly. That synergy between our manufacturing units and installation crews makes a huge difference on the construction site.
6. Custom to the Core
Early on, Legacy decided building off-the-shelf, prefabricated fabric structures was not a good fit for the innovations we were trying to implement.
Instead, we decided to custom-design each building to the client's needs. No two clients are the same, and no two projects are the same. The three things that people assume about customization are:
- It’s expensive
- It’s time-consuming
- The quality is compromised
We knew our challenge as a company was to address the issues of cost, time, and quality regarding our customized structures. Some construction companies use customization as an excuse to charge a lot and tack on add-ons as the project progresses.
We decided to combat that with transparent up-front design and clear communication. For example, our design team will give you an exact price before you sign any contracts. Since we use our own crews to construct a building, our clients don’t get blindsided by costs from “subcontractors.” Likewise, we can control costs with Legacy fabricating steel and fabric building components.
Custom’s Connotation
Another fear is that choosing a customized building will take forever to complete construction. We covered how our installation crews can finish a project so quickly. In the same way, Legacy’s design process allows us to tailor each building for our clients without adding cost or time to the process.
One of the primary reasons Legacy Building Solutions was established was to introduce a new standard for quality in building tension fabric structures. We saw improvements that could be made to fabric buildings, and we made them. Even though every building we create is different, we will not compromise on the fundamental components of every structure. That’s why our clients trust that the custom structure they order will meet or exceed their expectations for quality materials, engineering, and construction.
See: Custom Story—Fox Creek Sports Multiplex, Fox Creek, Alberta, CAN
7. That’s Fab(rication)
Bringing all aspects of our tension fabric structures in-house has been part of our evolution.
We began with the fabric plant, welding our own fabric panels for walls, roofs, end walls, and liners. Then we began fabricating our own steel beams for the frames. Finally, in 2019 we built our paint shop where we apply our proprietary epoxy coatings.
Add to that our own installation teams, and you can see the complete logistics chain that Legacy controls. There can still be speed bumps in the process, such as weather and pandemics, but we have ironed out as many operational elements as possible to deliver what we promise to our clients.
Finally, having our own design and engineering team to get the ball rolling is vital to creating a complete project because, in a few cases, the ability to turn around a project quickly has made all the difference.
8. Industry Standard
Legacy serves a lot of industries and sectors.
We began with bulk storage and agricultural storage and then branched out from there. We currently create structures for the following industries:
- Agriculture Storage
- Automotive
- Aviation
- Bulk Storage
- Energy
- Equestrian
- Military
- Mining
- Municipal Agencies
- Oil and Gas
- Recycling
- Salt Storage
- Sports
- Waste
Over the past thirteen years, we’ve learned a lot about each industry by working with their clients.
9. Quality Over All Else
In 1979, Philip Crosby, an expert in the Total Quality Management movement, wrote a book called “Quality is Free.”
What he meant by that is when a company spends time or money to improve quality on the front end of their processes, it pays dividends so quickly you earn back your investment almost immediately.
That has been the Legacy approach to design, manufacturing, and installation. All aspects of our business are reviewed under the ISO 9001 certification process yearly.
Seeing is Believing
Touring our headquarters is the best way to experience that. New employees are given a tour of the three plants: the steel plant, the fabric plant, and the paint shop. It’s where you begin to see how many innovations have been developed over our thirteen years.
10. & Everything Else
Our 10th lesson encompasses everything else:
Thank you for indulging us in our lesson summary. May each lesson we’ve learned help us navigate the future to better serve our clients and industries.
Have a Project In Mind?
Subscribe to our Blog
Recent Posts
- Speed vs. Quality in Commercial Construction: How Hybrid Materials Bridge the Gap
- Beyond the Bleachers: Designing Visually Striking Sports Facilities
- Why Architects Prefer Hybrid Steel Over PEMBs & Traditional Builds
- Building Innovations and Trends in the Mining Industry
- The Importance of Warehouse Storage for the Oil and Gas Industry